柴油发电机的单轴承主发电机一直采用传统安装方式进行安装试验,此种安装结构已经试验了100余种电机的型式试验及近万台主发电机试验,能够满足试验相关要求。该安装方式结构主要由拖动机、过渡支撑、被试电机及相关附件组成,被试电机通过试验支架和定子连接盘固定到试验平台上,转子连接盘与过渡支撑连接盘相连,从而达到模拟柴油发电机组的目的,详细结构因成本问题也很难实施,因此只能通过增如辅助支撑等措施来提高主发电机试验系统安装的稳固性。 如何解决试验安装方式中存在的轴系偏长和主发电机与试验台轴系的同轴度、端面跳动的问题,就成为解决振动速度值超差的关键问题,因此需要对原安装方式进行改进。针对2500kVA电机按传统结构方式安装后,试验过程中存在振动速度值超差问题,我们进行了分析,存在3方面的原因: (1)主发电机机座为焊接结构,强度、刚性稍差,在电机运行到额定转速时,造成主发电机试验安装结构发生颤振,引起电机振动速度值超差。 (2)从试验传动轴系方面进行分析,从过渡支撑轴承至主发电机右端轴承距离达到1750mm,轴系长度偏长,电机在被动旋转时,由于转子离心力的作用,轴系颤动加剧,造成电机振动速度值超差。 (3)在试验台上安装主发电机时,需进行主发电机和试验台轴系的同轴度和端面跳动调节,通常情况下轴系同轴度和端面跳动调整仅能达到0.2mm,该型主发电机采用的轴承是深沟球轴承结构,试验安装要求也较高,若要继续提高同轴度和端面跳动要求,在现有条件下已经无法满足,试验时造成振动速度值超差。
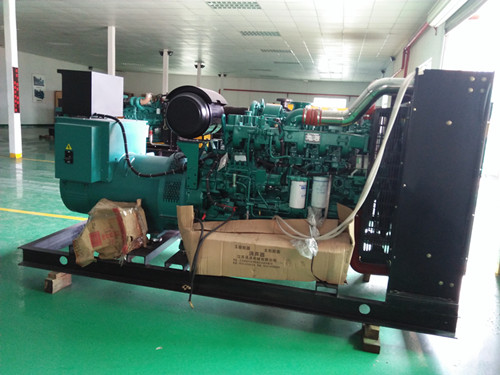
康明斯产品性能特点:
结构紧凑的柴油发电机组
皮带传动系统:带有自动张紧机构,使皮带免于保护
连杆:锻造连杆具有最大的结构强度
曲轴:经感应淬火锻造而成的钢制曲轴具有最大的强度和多次重磨能力
缸体:新型高强度设计使缸体的刚度提高32%,具有极高的耐久性
缸套:荣获专利的中止口设计使缸套具有最大的刚度,提高了活塞环的寿命
燃油系统:采用Bosch优质直列柱塞或转子高压油泵和喷油器,具有更高的燃油经济性
涡轮增压器:全部采用Holset增压器,HX40型带整体式废气旁通阀,进一步改善低速反应及动力性
活塞:铝合金活塞镶有两道耐蚀高镍铸铁环槽,提高了活塞和活塞环使用寿命,阳极化处理的活塞顶也有助于提高其耐久性
机油滤清器:组合式全流和旁通弗列加品牌,滤清效果近乎完美,提高了总机耐久性
北京发电机组厂家直销,发电机租赁,价格优惠,常年现货供应3-1500KW各产发电机组。咨询热线:13810484876